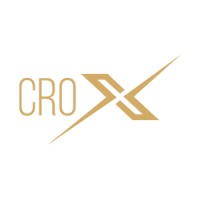
Environment, Health and Safety Manager
Location
Anaheim, CA
Level
Manager
Department
Type
Full - Time
Salary
$140,000-$150,000
Job Description
Posted on:
October 29, 2024
This position reports to the Manufacturing Director for the company business unit with full responsibility for day-to-day Environmental, Health and Safety at the Brea facility. Directly supervises two employees and indirectly guides the “safety committee” and production supervisors as safety champions.
Responsibilities
Primary Responsibilities
- Establishes, implements, and oversees environmental, health and safety programs to ensure facility compliance with all state and federal regulations including Cal/OSHA and local laws.
- Own and develop an overall safety and risk management program for the Company facility providing suitable loss prevention attention in all areas/levels.
- Host plant tours for audits and inspections to identify and correct potential hazards/exposures for full compliance with safety/environmental regulations.
- Pro-actively recommend policies, develop safety programs and coordinate initiatives throughout the factory and office areas.
- Applies regulatory and company policies/programs to ensure safe and environmentally sound working conditions.
- Engage Production Supervisors in participative groups as SPONSORS and messengers of the Safety values of company.
- Partner with Human Resources for employee training, health procedures pertaining to accident prevention programs, return to work issues, and coordinating time loss issues with payroll.
- Identifies and analyzes workplace hazards, health risks, prescribes necessary preventive or corrective measures and safety equipment.
- Contracts with vendors for properly licensed hazardous disposal and monitors waste handling.
- Organizes and equips spill-control teams. Reviewing, updating and maintaining environmental and spill-control manuals and procedures.
- Specifies/approves the purchase of safety and health products and services.
- Recommends external technical/advisory service providers.
- Sets safety standards for specific equipment and areas of operation.
- Researches loss, accident and illness frequency trends by area or operation, and initiate remedial action as warranted.
- Educates personnel in existing hazards, develops safety consciousness and assists with developing safety training recommendations. Personally delivers training or coordinates through industry groups and consultants as appropriate.
- Train production supervisors as safety SPONSORS.
- Ensure employee job instructions include PPE, safety, cautions and visibility
- Conduct employee hazard communication (right to know).
- Conducts respirator fit testing and other medical testing as required.
- Develops creative, motivational communications and training techniques to keep safety top of mind throughout the facility.
- Conducts periodic safety inspections of the facility, prepares reports, studies accidents and causes.
- Monitors housekeeping practices with a daily walk of the plant.
- Engage supervisors to investigate accident root causes. Solutions should seek to maintain control of hazards occurring from changes in processes, methods, materials, equipment or manpower. Ensure follow-up.
- Inspects fire sprinkler system monthly, insures that fire extinguishers are routinely checked, monitors new chemicals received, maintains current MSDA files for all chemicals and distributes list to impacted departments.
- Reports to management all accidents, health issues, major unsolved problems as they surface. No surprises is the goal.
- Conduct quarterly plant safety audits and reports results to management with recommended corrective actions.
- Maintain the highest ethical standards, even when challenged from above
- Understand and live by company ethics and business conduct policies
- Performs other duties as needed or as assigned by management.
Job Requirements
Qualifications
- Seven or more years EH&S experience working with AQMD, Title V, EPA and Cal/ OSHA in a manufacturing environment with more than $50 million in revenue.
- Sound technical skills as demonstrated by an understanding and practical application of technical knowledge in a leadership role with ability to articulate technical issues at an understandable level to a variety of stakeholders across the organization.
- Ability to work effectively in an environment where tact, sensitivity, respect, tenacity, persuasive ability, and decisiveness are required for success
- Strong writing, speaking, analytical and presentation skills
Competencies
- Customer Focus - Knows and understands the needs of internal and external customers. Is results oriented and works hard to consistently provide exceptional service.
- Ethics and Values - Adheres to an effective set of core values and beliefs and acts in accordance. Rewards the right values and disapproves of others.
- Problem Solving - Looks beyond the obvious to find effective solutions.
- Integrity and Trust - Widely trusted and seen as direct and truthful.
- Functional/Technical Skills - Possesses the skills to be effective in the job. Has the skills to perform the job at a high level of accomplishment.
- Listening - Practices active and attentive listening, able to hear others.
- Action-oriented - Full of energy, willing to take action.
- Composure - Cool under pressure, not knocked off balance by the unexpected, is a settling influence.
- Values Diversity - Supports fair and equal treatment for all.
Education/Previous Experience Requirements
- Undergraduate degree in Safety, Environmental or Engineering discipline is required
- Minimum of seven years of experience in Environmental Compliance and Safety in a manufacturing operation.