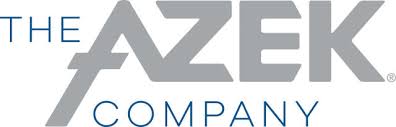
Environment, Safety and Health (ESH) and Lean Engineer
Job Description
Our compensation reflects the cost of labor across several geographic markets. The annual salary for this position ranges from $96,600 in our lowest market up to $125,400 in our highest market, plus bonus, equity, and benefits as applicable. The pay for roles at AZEK varies depending on a wide range of factors including but not limited to the specific work location, role, skill set, and level of experience.
Responsibilities
Responsibilities and Duties:
- Provide oversight and act as a resource for OSHA, ANSI, ASTM, NFPA, etc. for ESH capital project work and other construction activities.
- Comprehend and interpret regulatory requirements (e.g., OSHA, NFPA, EPA, etc.).
- Participate in Incident and Near-Miss investigations, evaluate root causes of these events, make recommendations for prevention based on best practices.
- Follow-up on Investigations:some text
- Final Root Cause was determined
- Corrective Actions implemented and follow-up on items not completed
- Perform ESH compliance audits to identify opportunities for improvements and provide recommendations for corrective actions as needed.
- Must comply with all applicable federal, state, and local regulation.
- Follow up using good management techniques to ensure problems are resolved.
- Establish strong working relationships with operations and support staff, relevant managers, and consultants.
- Compile, analyze, and interpret statistical data related to occupational illnesses and incidents.
- Ensure all Team Members, both hourly and management; receive all required ESH training necessary to perform their respective duties. This includes training for managers on ESH programs they are required to implement.
- Act as a coach and mentor to new and existing Managers, Supervisors, etc. in ESH Leadership
- Monitor the ESH corrective action logs in Cority to ensure all items are being corrected in a timely manner.
- Maintains and manages environmental compliance, permits, and inspections, which includes, but are not limited to NPDES, storm water, air quality, hazardous waste, residual waste, etc.
- Communicate and implement ESH best practices across the organization.
- Perform and prepare Job Hazard Analysis (JHA’s)
- Identify continuous improvement opportunities throughout the tactical level by routinely studying the GEMBA, reviewing site metrics, gathering Voice of the Customer data, etc.
- Plan, schedule, and execute the projects in the Lean funnel to drive improvements through the hierarchy of Safety, Quality, Delivery, Cost (SQDC), and Productivity.
- Promote a performance mindset at the Gemba level through Lean events, standardization, and simplification initiatives.
Required Skills:
- Teamwork - must be able to lead a team(s) AZEK employees from multiple disciplines and/or companies during the Incident investigations and Lean events.
- Ability to influence others - must be able to inform, convince, and persuade others to action on key initiatives.
- Results orientation - must deliver results and track sustainment.
- Technical excellence - must possess the technical skills necessary to be seen as credible in AZEK by peers and AZEK leaders.
- Communication - must be able to effectively communicate in both written and verbal forms. Able to discuss differences openly and influence others.
- Lean Skills - Green or Black belt trained. A working knowledge of Lean Principles and the ability to train others. Able to facilitate groups – Meetings/Training/Workshop setting.
- Software - Comfortable using Excel, Visio, Word, PowerPoint, SharePoint.
Job Requirements
Qualifications:
Must be hands-on and detail-oriented but also able to see the big picture. Need to be able to think strategically and view the business from a team leader or manager standpoint. Must be very customer-focused and have strong interpersonal and communication skills. Will need to be a quick study who can rapidly adapt to AZEK’s culture and gain the confidence of the AZEK organization. Will be an independent worker, capable of operating in a fast-moving, ever-changing environment, and able to effectively deal with difficult situations.
Required Experience:
- Bachelors in environmental, safety or related field
- 3+ years of experience in a manufacturing environment
- Proficient in Lean principles, methodologies, and tools such as A3 Problem Solving, Value Stream Mapping, Kaizen, 5S, Kanban, etc.
- Excellent interpersonal communication and leadership skills required
- Proficiency MS Office products such as MS Word, Excel and PowerPoint
- Excellent organizational and writing skills are a must
- Must be detail oriented